Impulse
1500mm EPP
Crash Resistant Sports Aerobatic Slope Soarer
Designed
by Stan Yeo
Produced
by PHOENIX MODEL PRODUCTS
Introduction
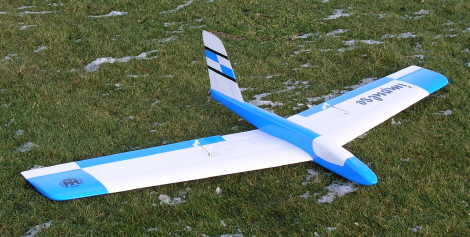
The Impulse
is a stylish, high performance, crash resistant, sports aerobatic slope
soarer designed to meet the ever increasing demands of the discerning
everyday sports flyer. It will do all manoeuvres expected of a flying
wing i.e. sustained inverted flight, loops, rolls and bunts etc., and
more besides such as a bun-roll (an outside loop with a roll at the bottom).
Few models claiming to be aerobatic slopers can do this manoeuvre let
alone a flying wing! Despite this the Impulse is a graceful docile model
to fly and will thermal turn with the best of them.
As with
all flying wings a control mixer is required to mix the elevator and aileron
controls. Although this can be done using an on-board mixer better control
set-up will be achieved using a computerised transmitter. Please do not
attempt to use plastic geared servos - they do not last long in EPP models!
Whilst our
EPP models are a little more complex than most of their contemporaries,
hence the performance, building time has been kept to a minimum and typically
a quarter to a third that of an equivalent wood foam model.
Tools
/ Materials Required
The only
tools required are a modelling knife and spare blades, 180 grade Wet &
Dry sanding block, a set square, soldering iron and a hand drill with
a 5mm bit. Glues required are spray impact adhesive (Stikatak), runny
super glue and 12 minute epoxy. Please observe safety precautions!
R/C
Equipment
The
R/C Equipment used in the prototypes consisted of two metal gear micro
servos (HS81MG / 85MG) a 2/3 AF size Rx flat Nicad pack plus a JR R700
/ Hitec Slimline / Webra 6 / Futaba 147F Rx. All the items are available
from PMP at competitive prices. 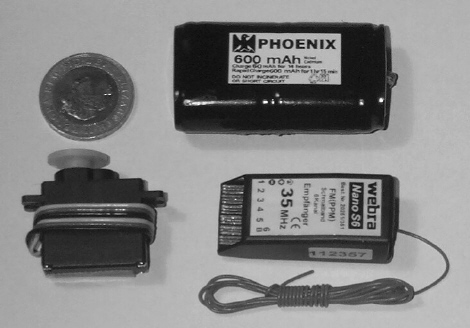
Building
the Fuselage
- Lightly sand the fuselage sides, top and bottom with 180 grade wet
and dry to remove the 'release' agent. Remove dust with a small brush
or vacuum cleaner.
- Mark position
of 4.5mm distance pieces to fuselage sides ensuring you have a left
and right side!
- Superglue
4.5mm sq. strip and triangular nose strips to fuselage sides.
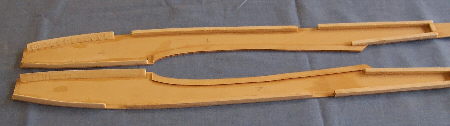
- Superglue
wing seats in position.
- Superglue
nose former and the other four 4.5mm distance pieces to one fuselage
side ensuring they are all perpendicular (use set square). Check dowel
former can be slid in position.
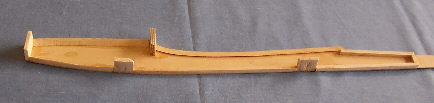
- Join fuselage
sides together over plan checking that the fuselage sides are correctly
aligned using set square.
- Cut 1.5mm
fuselage top to length and superglue in position.
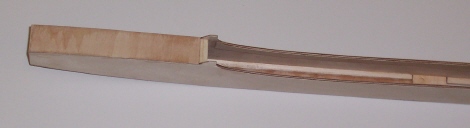
- Repeat
Step 7 above for fuselage bottom allowing for wing dowel plate.
- BUILD
WING
- Construct
Wing Nut block assembly as per plan. Slide into and hold in place with
scrap foam rubber. Slide into position the 6mm ply Wing Dowel plate.
- Fit the
wing to the fuselage and mark position of wing dowel hole on dowel plate.
Tip - wet end of dowel tube with felt tip pen to leave impression on
dowel plate. Ensure dowel hole is in middle of dowel plate and drill
dowel hole. Do not allow centre of dowel hole to drift towards bottom
of fuselage as this could prevent wing fitting snugly in wing seat.
- Superglue
dowel former in position. If necessary, slide former 'in & out' as appropriate
to compensate for any inaccuracies in drilling dowel hole.
- Fit triangular
strip to front of former (see plan).
- Fit wing
to fuselage and locate position of wing nut assembly.
- Glue nut
assembly in position.16Glue
EPP sheets to fuselage sides using spray adhesive (spray both surfaces).
Allow a couple of minutes for solvent in adhesive to evaporate before
fitting EPP to fuselage. Allow the EPP to extend past the nose former
by at least 12mm (see plan). Also remember this is a ONE shot operation!
- Trim
the EPP to shape of fuselage using White Spirit to lubricate knife.
The best tool for this operation is one made from a broken piece of
hacksaw blade approximately a 75mm long. Grind the teeth off without
getting the blade so hot that it loses its temper and goes soft. Sharpen
blade on a whetstone or oilstone so that you could almost shave with
it! The advantage of this blade over commercial blades is that it is
flexible allowing the 'handle' to be bent out of the way when cutting
the EPP to achieve an acute cutting angle.
- Fit 6mm
square strip to base of Fin at front.
- Glue Fin
in position checking that is perpendicular to fuselage.
- If applicable
fit optional 3mm dia. Carbon rods in the Fin (see plan).
- Glue
plastic aerial tube / Fin fairing to Fin leading edge using impact adhesive
such as Evo-Stick. Tape in position until glue is set (24hrs).
- Glue 10mm
thick EPP to fuselage top again extending EPP forward of the nose former
and stopping at Fin base.
- Glue
8mm thick strip of EPP to fuselage bottom at nose. Again extending beyond
nose former.
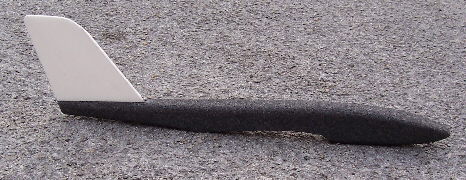
- Glue 10mm
thick EPP to rear of Fuselage and trim to shape.
- Using
spare 10mm thick EPP glue foam to base of Fin and trim to shape.Glue
approximately 150grams of roofing lead to front of nose former in cavity
formed by EPP sides. This is typically 2mm thick and equates to 5 layers
of lead. Flatten lead before fitting. Roofing lead is available from
the scrap yard at approximately £1.00 a kilo.
- Trim EPP
in front of nose weight to provide flat surface on which to glue EPP
nose-block.
- Fit nose
block and shape fuselage i.e. round corners using sharp knife and 180
grade wet & Dry (use dry!).
- Cover
fuselage using CW tape. Overlap each strip by 6 - 10 mm or 1/4 to 3/8
inch. Use Film Iron to remove wrinkles around compound curves. Temperature
required for this operation is fairly critical. Do not dwell in one
spot too long to avoid damage to the foam. Use white spirit to lubricate
cutting knife.
- Excess
impact adhesive can be removed using white spirit.
Building
the Wings.
- Lightly sand wing
surfaces and remove dust as before. Trim and sand spar slots to accommodate
mainspars. Unfortunately cutting tapered wings with spar slots result
in a tapered spar slot. Remove waste from wing bracing slots.
- Remove waste from
wing bracing slots.
- Fit top wing spars
using Epoxy keeping spar bracing slots free of Epoxy. Place packing
tape along spars, place wing on a flat surface. Hold flat with weights
until epoxy set.
- Trim spars to
length.
- Fit 6mm sq trailing
edges using epoxy again keeping bracing slots free of epoxy. Use masking
tape to hold spar in position whilst Epoxy sets. Trim to length.
- Dry fit bottom
mainspars and trim to size.
- With wing upside
down fit wing brace and bottom wing spars. Note trailing edges should
form a straight line i.e. not be swept back or forward.
- Fit rear spar
brace and trim to size when epoxy set.
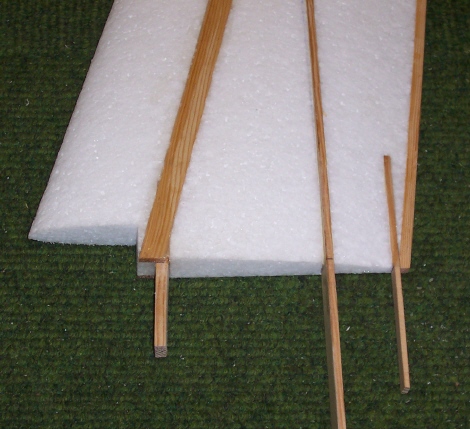
- Fit rear wing
brace using epoxy.
- Manufacture Elevons
and wing centre by laminating 0.8mm ply and balsa trailing using spray
impact adhesive. Place under weight until adhesive has properly set.
- Glue centre section
to wing observing wing reflex (apparent up elevator). Refer to wing
seat on fuselage.
- Fit 0.8mm ply
ends to centre section and one end of each Elevon.
- Sand wing tips
to shape and trim Elevons to size. Sand to shape.
- Epoxy balsa block
in position at wing join. Bottom of block should be flush with bottom
surface of wing.
- Trim top surface
of block to shape of top surface of wing. DO NOT trim bottom of block.
- Locate centre
of balsa block and centre of wing leading edge. Drill hole for 5mm diameter
brass tube the houses 4.5mm diameter hardwood wing locating dowel.
- Epoxy wing dowel
tube in place. Mark centre of tube hole on 6mm ply dowel locater in
fuselage. Use felt tip pen to assist in this.
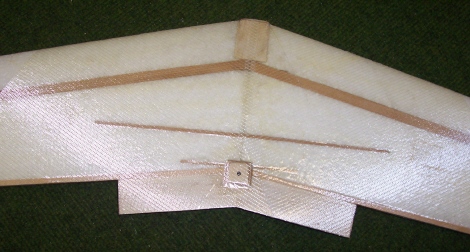
- Manufacture a
long drill using 4.5mm diameter piano and drill dowel hole in 6mm ply.
- Drill for M5 wing
bolt. Do not drill through rear spar!
- Fit 1.5mm ply
wing bolt reinforcement and drill hole for wing bolt.
- Construct Pronged
Tee nut housing as per plan and using wing to find correct position
glue wing nut plate assembly in position.
- Mark position
of wing servos (plan drawing is NOT full size. Position of servo is
dependant on servo lead length. Allow 30mm from end of plug to servo
lead exit from wing for connecting to receiver extension lead when fitting
wing. Note servo arms both point outboard of wing.
- Cut rectangular
hole for servo in wing ignoring servo mounting lugs.
- Cut slot in EPP
for servo lugs and fit servo so that it is flush with top of wing. Note
gap between top of servo and bottom of wing. From block of EPP removed
for servo from wing slice off the required amount and fit in this void.
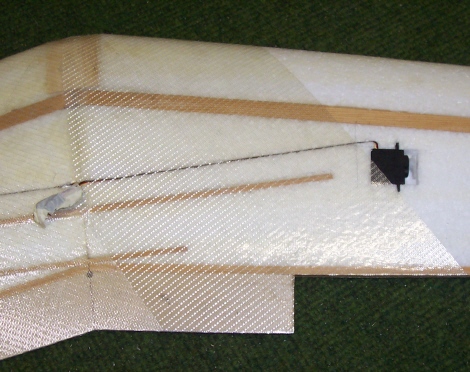
- Remove wing servos
for covering.
- Shape wing tips.
- Spray wing with
spray adhesive and cover wing with GW tape. For torsional rigidity cover
the wing with CW tape diagonally. There is no need to wrap around rear
spar but do overlap by 5 - 10mm at leading edge. For smooth finish do
not overlap CW Tape. Use film iron to remove wrinkles at tips.
- After covering
fit aileron servos. Cut vertical slot in wing to hide servo leads.
- Cover wing with
either coloured vinyl tape or an iron on polyester film (NOT polypropylene
it stretches!). This is necessary for two reasons, one to decorate the
model and secondly to protect the CW Tape from the effects of ultra
violet light. If film covering roughen surface of CW Tape a lightly
spray with impact adhesive.
- Cover Elevons
in an iron on film in suitable colour. DO NOT use CW or vinyl tape.
- Hinge Elevons
using Sellotape diamond as shown on the plan.
- Fit control linkages
and adjust to obtain required throws(see flying section).
- DO NOT replace
the plastic mini-snaplinks with metal devises. In the event of a mishap
the plastic snaplinks will break thereby reducing the risk of damage
to the aileron servos.
Flying
To achieve
the design performance of any model care must be taken in
setting up the controls and balancing the model both laterally (wing tip
to wing tip) and longitudinally (nose to tail). The Impulse is no exception.
Control movement must be symmetrical i.e. the same for both Elevons.
- Set the controls
to give the following movements for initial flights: Ailerons
+/- 18mm Elevons
+/- 6mm Balance Point 125mm +/- 3mm from LE at back of dowel former.
- Adjust
balance to within recommended limits. This can be done by taping a hexagonal
shaped pencil along the bottom of the wing at the balance point and
resting the model on a flat surface. Prototypes required a small amount
of additional nose-weight to that fitted in the nose.
- Check
than Fin is perpendicular to wing. Adjust wing seat as necessary.
- Launching
the Impulse is easy. Place the thumb and second finger either side of
the fuselage just in front of the wing leading edge. The forefinger
is placed on the underside of the wing. This is important as the forefinger
ensures the model is launched in a level attitude and stops you pulling
the nose down and launching the model into the ground! The transmitter
is naturally help in the free hand.
- Remember
all aerobatic manoeuvres require energy to perform them. If the model
has insufficient speed it will fall out of the manoeuvre or perform
it half-heartedly. Vertical or near vertical dives are not an efficient
way to build up speed, 20- 30 degree dives are much more efficient.
Avoid sudden control inputs. In most cases all they do is scrub off
speed and lose height but they could also result in a violent 'flick'
roll. Try to fly smoothly with the minimum of control input as not only
do the manoeuvres look better but you will be able to perform more of
them before having to regain height. Try stringing manoeuvres together,
paying particular attention to positioning. Be creative and set yourself
targets for each flying session.
- If the
lift is very good or you are having difficulty penetrating into wind
try ballasting the model. This will increase penetration and help the
model maintain speed through manoeuvres. Note when adding ballast take
care not to disturb the balance point. We have found the optimum ballast
to be about 200 grams. Over-ballasting any model will lead to a degradation
in its performance, often accompanied by a tendency to tip stall.
- The suggested
control settings are a starting point and can be adjusted to suit your
personal tastes. An indication that the balance point is about right
can be gauged by the amount of down elevator required for smooth inverted
flight and how the model recovers naturally from a dive i.e. sticks
in neutral and no pilot input.
- If you
are using a computerised transmitter program in positive (JR) Exponential
on the Aileron and Elevator controls. This will 'soften' the controls
around the neutral position and facilitate smoother flying particularly
on the elevator control.
- Impulse
will take a lot of punishment. It is excellent for building confidence
and will add another dimension to your flying but please remember if
you take a big enough hammer to anything it will break. The CW tape
used for covering also degrades in ultra-violet light so store the model
in a relatively cool place away from direct sunlight.
- The MH64
wing section is very efficient and performs well in light lift so with
good ballast selection Impulse will cope with almost wind / lift conditions
you are prepared to fly in.
- Finally
should you require further assistance or advice please contact us either
by letter, telephone, email or visit our website (http://www.phoenixmp.com)
where you will find useful information on sloping etc.
Impulse
Design Features
- It uses the highly
efficient MH64 wing section.
- It has an ultra
slim, EPP clad, ply box fuselage. Not only is the fuselage extremely,
strong overcoming the detaching nose syndrome of other similar designs,
but it also has up to 50% less cross-sectional area than most if its
contemporaries. Fuselage volume has a large impact on a model's performance.
The more air that is displaced the higher the drag!
- The Impulse is
a two piece model. The wing is attached to the fuselage via an easily
replaceable M5 nylon bolt and a 5mm hardwood dowel (housed in a brass
tube). These are designed to shear in the event of a 'mishap thereby
minimising any resultant damage.
- The Impulse has
excellent directional stability. This is due to the combination of a
generous fin area coupled with a respectable tail moment arm and the
almost flat fuselage sides. Round fuselages look good and are arguably
more streamlined but do not offer much resistance to the air to counteract
any tendency to 'fishtail' or aid spin recovery.
- The hardwood mainspars
extend all the way to the wing tip. This not only stiffens the outboard
section of the wing but offers protection to the control surfaces should
the model land on a wing tip.
- The top spar is
thicker than the bottom spar. This significantly strengthens the wing
as most wing failures in flight are due to the top surface failing in
compression.
- The leading edge
of the Correx fin is dressed with a 4mm diameter plastic tube. This
not only provides a fairing for the fin leading edge but acts as a conduit
for the receiver aerial improving reception (better aerial positioning).
- The thin balsa
control surfaces are laminated with 0.8mm ply to add stiffness and make
them more 'ding' proof.
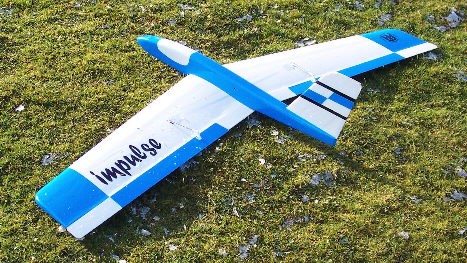
Happy flying,
safe landings
Stan Yeo
Impulse 050306
|